The Importance of Air Compressor Redundancy
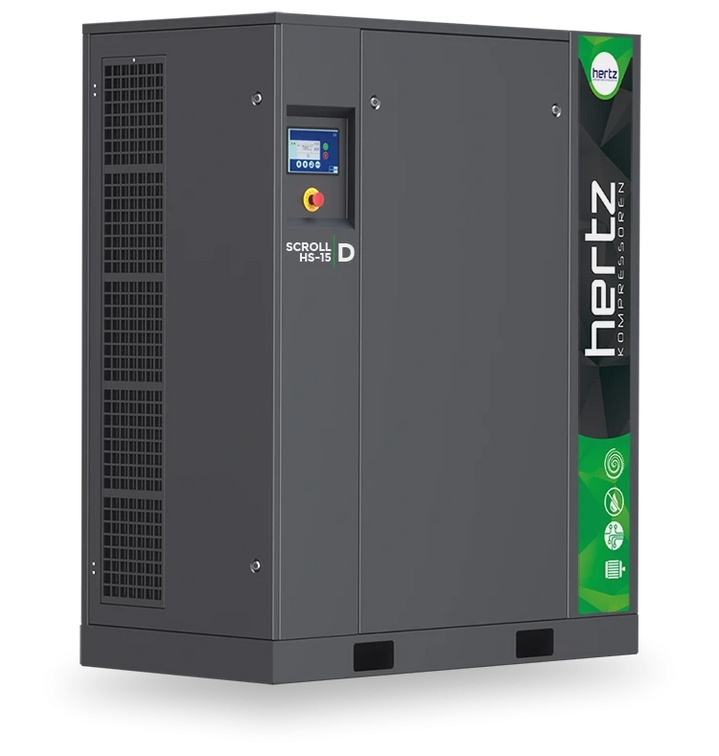
Air compressors are essential for many machines, including grinders, dust collectors, and lasers. These systems draw in air from the surrounding area, reduce its volume, and force it into a pressurized holding tank for later use. When the pressure reaches a set limit, the compressor shuts off.
Pressurized air is valuable for many applications, particularly in industrial settings, so operations that use a great deal of air to maintain productivity need to have a reliable supply. Many times, the best solution is air compressor redundancy — having two or more compressors working in parallel and operating in tandem to meet demand.
Benefits of Air Compressor Redundancy
Allowing multiple air compressors to take turns and share a workload provides:
- Emergency availability: Secondary air compressors operate in parallel with primary compressors and take over the entire load if the primary compressors fail. The backups allow you to keep your facility running and meet operational demands.
- Minimized downtime: Businesses can schedule air compressor services at any time without having to shut the facility down or pay extra for an after-hours visit. One compressor keeps your operation going while the other is serviced.
- Less wear and tear: Compressors will begin to age and become less efficient over time. Implementing air compressor redundancy can help extend the longevity of your mechanical components and yield savings on maintenance or replacements.
What Can Cause Air Compressor Failure?
Proper planning and establishing a maintenance routine can help keep a compressed air system’s mechanical components running as they should. In most cases, potential issues or failures result from:
- Overheating: Overheating may happen if a work environment is too humid and hot, the vents for the room are obstructed, or a structure blocks the airflow around a machine. In other cases, clogged air filters or dirty oil lines may cause friction and burnout in a compressor’s internal components.
- Bearing failure: Compressors’ bearings need regular oil changes, and their motors need greasing. Without proper lubrication, the components can degrade quickly and cause a premature system failure.
- Exceeding design limits: Air compressors have limits you should not exceed. If you use more air than your mechanical components can provide, ineffective discharge pressure and low energy efficiency can eventually result in compressor failure.
Ensuring that production is not interrupted due to scheduled maintenance or unforeseen failure helps keep production schedules and customer deliveries on time.
Signs You Need Air Compressor Repairs
Preventive maintenance offers a way to identify potential issues early on, prevent costly damage, and minimize downtime at your facility. Consider the staggering costs if your air compressor were to break down for 8 hours or more — the lost production, the missed shipments, the unhappy customers, and the emergency repair bills could easily add up to thousands of dollars.
Trained technicians can conduct a detailed inspection of your system and provide an overview of any air compressor services needed. Outside of routine inspections and maintenance, there are signs that can indicate the need for air compressor services. You should schedule repairs for the mechanical components if you notice the following:
- Air leaks: Have you noticed air leaks around your unit? Air leaks could indicate a faulty part that needs replacement.
- Low pressure: Do you have low pressure at the air compressor discharge? Low air pressure may indicate that your unit is worn out and needs replacement.
- Excessive oil: Have you noticed excessive oil in discharge air? Air compressors that aerosolize too much oil may damage attached tools or accessories. If your operation relies on high-purity air, prompt repair for this issue is crucial.
- Strange sounds: Can you hear clicking, rumbling, rattling, or vibrating? Excessive noise may indicate there is an issue with the air compressor that requires repairs.
- Slow or no starts: Does the air compressor seem sluggish or refuse to start up? Air compressors that do not work efficiently may need an inspection to identify ways the system can improve with repairs or replacements.
When considering an air compressor service provider, look for a highly trained team with decades of experience serving businesses in your industry. Choose a partner that provides products and services aligned with your operational needs.
Contact Liberty Systems for Air Compressor Solutions
If you are looking to upgrade your air compressors or have your components serviced, Liberty Systems can provide dependable solutions. Our company is a knowledgeable industry leader in nitrogen generation. We have over 20 years of experience helping customers in the metal fabrication industry increase their productivity and reduce operational costs.
When you partner with us, you will receive unmatched support from our Service Engineers. Our team can answer any questions you have and offer guidance on choosing the best products for your application. All our systems are tested in-house before shipping. When our technicians arrive to complete the installation, they will train your team on the system’s operations and service requirements.
If you suspect your air compressors are not working as they should, we can provide any repairs or replacements you need. Our technicians use industry-best techniques to service all makes and models of generators and equipment, including Ozen air compressors. We will ensure your system is running efficiently to maintain productivity at your facility.
To learn more about our offerings or schedule services for your air compressors, contact our team today.